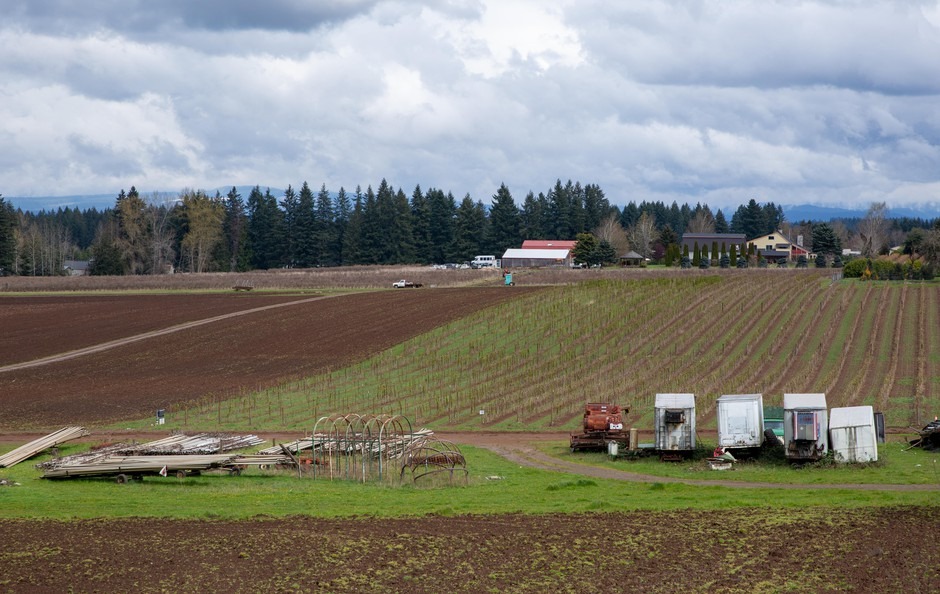
COVID-19 Considerations Sprout Confusion, Uncertainty To Northwest Family Farms
Listen
BY COURTNEY SHERWOOD / OPB
The strawberries have just begun to bud at Liepold Farms, in Boring, Oregon.
If this were a normal year, brother and sister Jeff Liepold and Michelle Krummenacker would be tending the grounds and preparing for early May harvest, just as their parents and grandparents did before them. But as with many things in the era of COVID-19, this year is far from normal.
For the first time in this third-generation family farm, it’s not clear if the migrant workers who harvest strawberries each spring will be allowed to travel north from California to work the fields. And if those fieldworkers do arrive, Krummenacker said, the family does not know how it will sell its prized Hoods this year — or whether one of the farm’s biggest customers will still be buying its other Oregon-grown fruits.
“I think people take it for granted when you go to the store, like, ‘Oh, there’s food here’ — and it takes a lot of time, energy and work to get things from our field to that place,” she said.
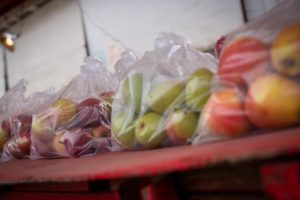
Apples for sale at the Liepold Farms produce stand in Boring, Ore., on Friday, April 3, 2020. The produce stand, which sells the farm’s organic berries in season, operates for about 10 months out each year. CREDIT: Bryan M. Vance/OPB
Across the Pacific Northwest, small and mid-sized farms are grappling with a range of challenges brought about by the novel coronavirus.
In eastern Washington, potato farmers are planting less as demand for restaurant french fries evaporates, and apple growers are worried about a drop in overseas exports. In Hood River, Oregon, tree fruit farmers have led Spanish-language training on social distancing and they’re worried about selling this year’s harvest. And at a dryland wheat farm near Helix, Oregon, the owner said he’s in better shape than many of his peers, with almost no impact from COVID-19.
The good news for Northwest consumers: Despite all the uncertainty affecting growers across the region, experts say the food supply is sound, with growers in California and Florida reporting abundant crops. The supply chain, on the other hand, has been challenged. Growers used to selling to restaurant chains and school cafeterias have been unable to quickly pivot to sell to supermarkets instead. Access to freshly harvested local fruits and vegetables from small and medium-sized farms? That is not a sure thing.
“Many people are worried about a possible recession or even an economic depression stemming from COVID-19, and the agricultural industry is not immune from that, by any means,” said Samantha Bayer, an attorney who specializes in policy with the Oregon Farm Bureau. “The agricultural industry has essentially been in a recession for the last three to four years because of declining market prices and regulatory overhead, and many producers may not survive the effects of COVID-19.”
It’s hard to know which of the financial challenges that have presented themselves to Liepold Farms is the most pressing. There’s the push to upgrade conditions for fieldworkers; new packaging and food safety standards from fast-food chain Burgerville, one of the farm’s biggest customers; and uncertainty around farmers markets amid social distancing and hygiene concerns.
“There are so many things coming in to play that we are reeling, really,” said Marcia Liepold, Krummenacker’s mother. “It’s just mind boggling to put this all in order.”
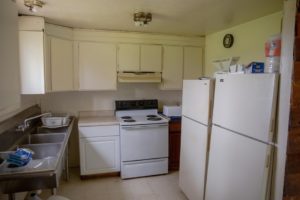
The communal kitchen in one of the migrant worker housing units at Liepold Farms in Boring, Ore., on Friday, April 3, 2020. CREDIT: Bryan M. Vance/OPB
The biggest unknown facing Liepold Farms and other farms across the region comes in the form of a petition that advocates for low-income and immigrant communities submitted to Oregon OSHA in March. The Oregon Law Center and Virginia Garcia Memorial Health Center asked for more portable toilets and hand-washing stations in fields — one for every five workers, instead of one for every 20, as required today. They also asked for upgrades to migrant housing, including vacant spaces dedicated to housing any workers who get sick while on the job.
“If they require a sink for every five people, if we have a crew of 60, are we going to have 11 or 12 washing stations that cost $400 to $500 apiece? And that’s just washing stations,” Liepold said. “And you can’t wait to the last minute to get these, you have to spend the money upfront.”
Other upgrades sought in the petition could cost $40,000 or more, Krummenacker said. Yet many years, the farm’s payout to its owners is only $50,000 or $60,000 after expenses, she said.
Pineros y Campesinos Unidos del Noroeste, or PCUN, a union for Oregon farmworkers, has focused its COVID-19 advocacy on job protections, access to health care, and sanitation advocacy such as deep-cleaning of immigrant housing, rather than on the specific investments requested in the OSHA petition.
Reyna Lopez, executive director of PCUN, said that immigrant workers depend on economically viable farms to be able to make a living. But they still need to be protected.
“Oregon is one of the most vibrant agricultural economies in the world, and for us that would mean devastating effects to have our agriculture industry knocked down by COVID-19,” she said.
Oregon OSHA administrator Michael Wood told OPB he’s gathering feedback from farms and considering the health needs that farmworkers face. He expects to act quickly on the petition.
“Given that this petition comes up specifically in the context of the COVID-19 outbreak, it does not allow us to use as deliberative a process as we normally would,” Wood said. “And if we move forward with rule-making, it wouldn’t make sense to do our normal practice of providing 60 to 180 days, or sometimes even a year, between rule adoption and the effective date. If we do this, it is something we’ll need to have come into place quickly.”
Until then, Liepold and Krummenacker do not know what — if anything — to do to prepare for workers who typically begin the strawberry harvest in May.
Liepold Farms is also facing changes from Burgerville, which is one of its largest buyers. The fresh fruit in the fast-food chain’s strawberry and raspberry shakes, and its seasonal marionberry products, all come from the family farm.
“Historically, we’ve been able to pick fresh and deliver berries to a site that redistributes to all their stores with a fresh-packed product,” Krummenacker said. Within 12 hours, fresh berries go from farm to customers.
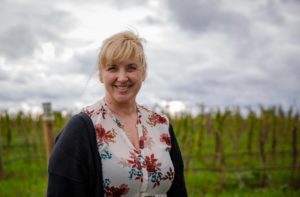
Michelle Krummenacker, whose family has owned and operated Liepold Farms since the 1950s, poses for a portrait in front of some of the farm’s raspberries in Boring, Ore., on Friday, April 3, 2020. CREDIT: Bryan M. Vance/OPB
But Burgerville recently informed the farm that it wants to add a middle step to ensure food safety along the way. That might work for shelf-stable berries grown on large corporate farms, but the berries Liepold Farms grows have been bred to be at their peak flavor within three days of harvest. Delaying delivery to the fast-food chain could put an end to sweet and flavorful Liepold-grown berry shakes, Krummenacker said.
With so much uncertainty about even the next few weeks, Krummenacker and Liepold said plans to pass ownership of the family farm on to the next generation may have to be put on hold for several years.
“We worked so hard to keep our farm,” Liepold said. “This year we were supposed to be retiring. This has thrown that off.”
Yet not all agricultural operations in the Pacific Northwest have been equally hard hit.
Matt Wood — who lived in migrant housing and worked on berry farms earlier in his life — now grows dryland wheat and hay on 2,000 acres outside of Helix, Oregon.
Unlike irrigated fruit and vegetable farms, dryland wheat fields require very little labor. Wood and his son can provide most of the work the farm requires, so they do not have to worry about migrant housing or social distancing.
And unlike fresh Hood strawberries that peak within days of harvest, wheat can be stored indefinitely, and hay can be kept for years.
“Most of the wheat that’s grown in the Pacific Northwest is delivered to the Asian market, which would be China, Japan, Korea, Vietnam, etc.,” Wood said.
The U.S.-China trade war has suppressed sales, he said, but coronavirus has not. “I feel lucky that so far the COVID-19 has had very little impact on our operation.”
Occupying the middle ground between vulnerable berry farms and more resilient wheat farms are operations like McCarthy Family Farms, which grows peaches, pears and cherries in the Hood River area.
Mike McCarthy said he has offered training in Spanish and sent out written information to workers based on U.S. Centers for Disease Control COVID-19 recommendations.
He’s watching OSHA’s deliberations carefully, and, like Liepold Farms, is worried about the spending he would have to do if new housing and hygiene rules are passed.
But he’s also concerned about a weak market for his produce, at a time when many grocery shoppers are stockpiling shelf-stable provisions like rice, beans and toilet paper instead. The restaurants that buy a big share of produce are shut down, creating a weak market for many farm-grown foods, according to trade publication The Packer.
“And so we have a fairly significant amount of our fruit that may not get sold this season because of this whole COVID issue,” McCarthy said. “This is the worst pear prices we’ve had in 40 years.”
Copyright 2020 Oregon Public Broadcasting. To see more, visit opb.org
Related Stories:
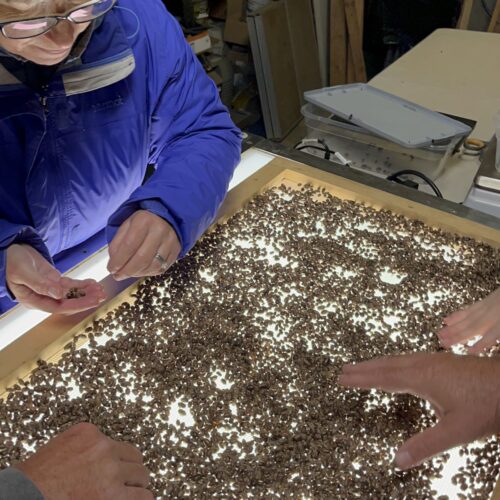
The dirty work of owning mason bees
Every October in the backyard of a Bothell home, a team of workers swarm around millions of blue orchard mason bees, to harvest the hibernating bees.
The company, Rent Mason Bees, quickly takes apart and cleans the wooden nesting blocks that gardeners and farmers across the state use in the spring to house these tiny pollinators. The company offers this service as part of its mason bee rental program.
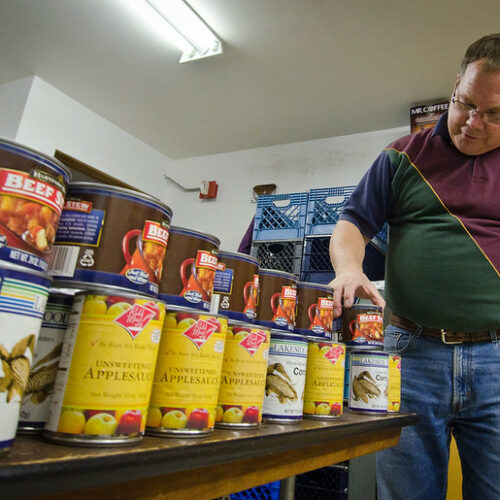
Rural areas hit hard by food insecurity, study finds
Joe Tice, the Tukwila Pantry’s executive director, stocks tables with canned goods at the food bank in Tukwila, Washington. (Credit: Lance Cheung / USDA) Listen (Runtime 1:03) Read Before she
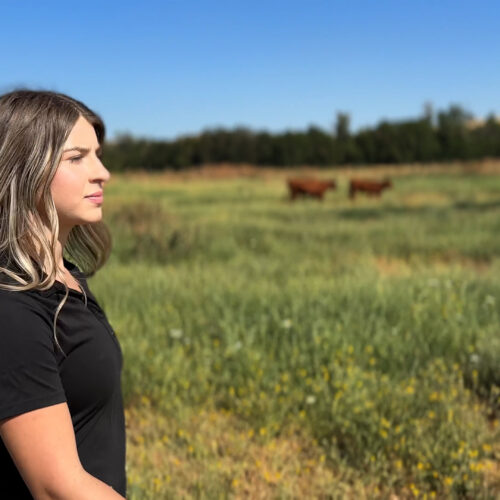
Walla Walla Community College buys land to grow its Farm to Fork program
Holland Gallaway, an agriculture student at Walla Walla Community College, with cattle owned and raised as part of the college’s Farm to Fork program. (Credit: Daniel Biggs / WWCC) watch